2, 5, 7 or 14 Lean principles? Which ones are "true" ?
How many Lean principles exist, 2, 5, 7 or 14? And which ones are the true Lean principles? Indeed, the Lean principles are defined in numerous books, publications and reference websites on Lean.
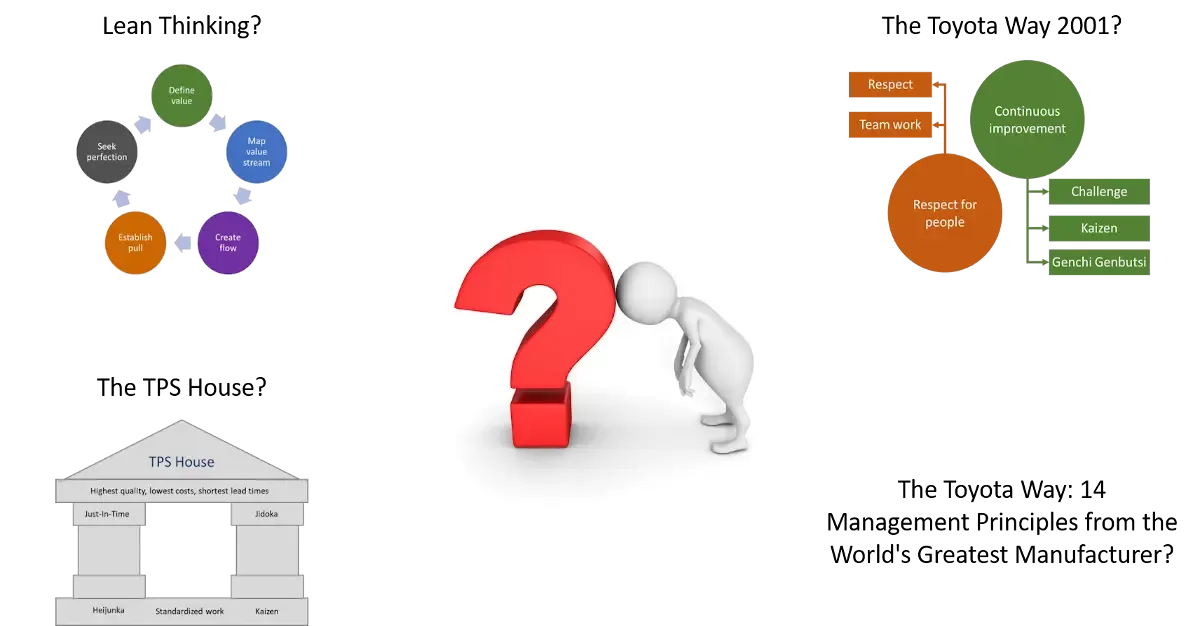
Lean principles of the "TPS House"
The famous "TPS house" diagram is the first model of the TPS system. It has five Lean principles or elements:- a three-element base
- Heijunka: smoothing of production, in volume or in product mix over a certain period of time, in order to reduce the consequences of purely on-demand manufacturing
- Standardized work: standardization of procedures to promote reproducibility of production and learning by staff
- Kaizen: continuous improvement
- two pillars
- JIT: Just-in-time
- Jidoka: sometimes called "autonomation", and has two meanings:
- detach or free the human from the machine (allowing him to supervise several of them)
- do not allow defects to pass through (machine stop), which creates a "Built-In Quality" system

The five Lean principes of "Lean Thinking" de Womack, Jones et Roos
James P. Womack, Daniel T. Jones, and Daniel Roos were the first to formalize the name and approach of "Lean" in their book "The Machine That Changed the World" published in 1991. They defined five Lean principles in their book "Lean Thinking" published in 1996
- Define value; value refers to all the characteristics or functions of a product or service that meet the customer's needs and for which the customer is willing to pay.
- Map value stream: value streamare the different sequences of activities required to design, produce and deliver a product or service to the customer, including information processing and raw material supply. Activities that do not add value to the customer are considered wastes. There are two types of wastes, those that are not necessary and need to be eliminated and those that are nevertheless necessary. An example of a necessary waste is quality control: the customer does not pay for quality control, but wants a reliable product and therefore control (or quality assurance) is necessary.
- Create flow: ensure that production is carried out smoothly, without interruption or waiting and eliminate all unnecessary losses; necessary losses can be reduced.
- Establish Pull: set up a downstream production system; each upstream production step is carried out at the request of the downstream step, starting from the customer. This makes it possible to limit stocks of work in progress as much as possible.
- Seek perfection: continuous improvement as a method to achieve perfection is fundamental in Lean thinking, this principle of continuous improvement must be part of the organization's culture.
The two pillars and five Lean principles of the "Toyota Way 2001"
In the 1990s, following a more widespread deployment of Lean and some failed implementations, some criticism emerged. Lean and the Toyota Production System seemed too technical without taking sufficient account of the human dimension. They were better known for the "Kaizen", "Kanban" or "standardized work" methods than for "respect for people". Fuji Cho, President of Toyota from 1999 to 2005, published in 2001 the "Toyota Way 2001". It officially describes the Lean principles (in fact the TPS principles for Toyota) with a definition more in line with reality as experienced by Toyota. In particular it highlights more clearly this human dimension which he considered essential.The "Toyota Way 2001" describes five Lean principles articulated within two pillars
- Continous improvement
- Challenge
- Kaizen
- Genchi Genbutsu
- Respect for people
- Respect
- Team work

"The Toyota Way: 14 Management Principles from the World's Greatest Manufacturer" by Jeffrey K. Liker
Jeffrey K. Liker is Professor Emeritus of Industrial and Operational Engineering at the University of Michigan; he has written numerous books on Toyota, including the one that is a Best Seller at over one million books, and has won more than 13 Shingo Awards for Research Excellence. In "The Toyota Way: 14 Management Principles from the World's Greatest Manufacturer" he identifies Toyota's 14 management principles, some of which are already outlined in the two previous paragraphs. These management principles continue some of the Lean principles already mentioned above:Part One: Long-Term Philosophy
- Principle 1 - Base your management decisions on a long-term philosophy, even at the expense of short-term financial objectives.
Part Two: The right processes will produce the right results
- Principle 2 - Create a continuous process flow to bring problems to the surface. (Just in time)
- Principle 3 - Use traction systems to avoid "overproduction".
- Principle 4 - Equalize workload. (Eliminate waiting)
- Principle 5 - Build a culture of "stopping to solve problems" to ensure quality. (Eliminate touch-ups)
- Principle 6 - Standardized tasks are the foundation for continuous improvement and employee accountability.
- Principle 7 - Use visual controls to ensure that no problems are hidden. (Opportunities are visible to all)
- Principle 8 - Use only reliable and carefully tested technologies to serve your people and processes.
Part 3: Adding value to the organization through the development of your employees and partners
- Principle 9 - Develop leaders who fully understand the work, live the philosophy and teach it to others.
- Principle 10 - Develop exceptional people and teams that follow your company's philosophy.
- Principle 11 - Respect your extended network of partners and suppliers by challenging them and helping them to improve.
Part Four: Solving root problems on an ongoing basis generates organizational learning
- Principle 12 - Go and see for yourself and understand the situation.
- Principle 13 - Make decisions slowly by consensus, fully considering all options, and then implement them quickly.
- Principle 14 - Become a learning organization through constant reflection and continuous improvement.
Other Lean principles
It can be said that the four previous definitions of Lean principles or Lean pillars of are the best known and established. However, other definitions have been created for applications in other fields. Two examples can be given:- The 7 principles of Lean software development in the book co-written by Mary and Tom Poppendieck "Lean software development" published in 2003
- 13 principles are defined for product development in another book by J. Liker "The Toyota Product Development System, Integrating People, Process and Technology" published in 2006
By searching well on the internet you can find many other definitions, but much less known if not sometimes a little fanciful.
What to do with all these Lean principles? Which ones are "good"?
If we take only the first four definitions, there are still a significant number. Even if the 14 principles of Lean of "The Toyota Way: 14 Management Principles" totally encompass those of the "TPS house", part of those of Womack's Lean and the "Toyota Way 2001".If we are to retain only one, we will retain the "Toyota Way 2001", for three reasons.
- it seems to us that the number of principles must be reduced in order to be easily communicated and retained by employees who must implement them.
- the principles must remain general enough not to be confined to a restrictive and undeveloped model. For example, the "Establish pull" principle may not be valid in all cases (many critics already agree); moreover, one could imagine that advances in artificial intelligence could lead to a superiority of a production mode that is no longer "pull" but predictive. In this case, if one of the principles of Lean is no longer true, is Lean no longer true?
- the principles are different from methods or techniques, it is preferable in our opinion that they concern human aspects, behaviours, ways of thinking, rather than techniques. This last point being one of the major criticisms that has been made of Lean.
Nevertheless, all these definitions and "Lean principles" they contain are very interesting or good, especially given their success. Not necessarily one is "better" than the other.
In our opinion, the main thing is to understand these different Lean principles and apply those that are most appropriate to your application case.
Stay Informed
When you subscribe to the blog, we will send you an e-mail when there are new updates on the site so you wouldn't miss them.
Comments 1
Been wrapping my head around SAFe topics like team demos and PI Planning. Found some cool quizzes on getsafecertified.com. Anyone else checked it out